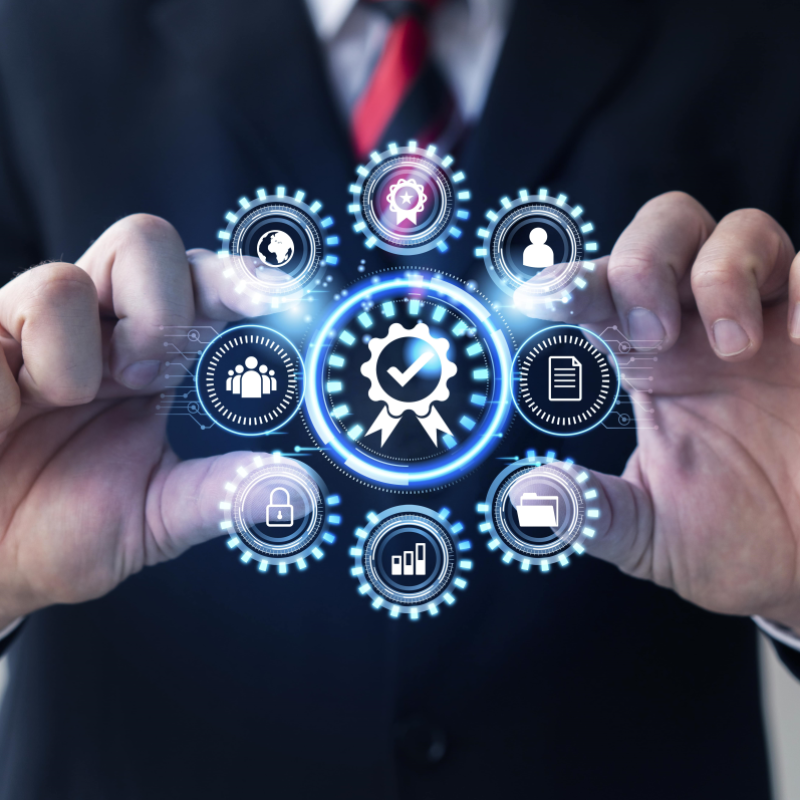
1. What is ISO and Why is it Important?
ISO (International Organization for Standardization) is an independent organization established in 1947, headquartered in Geneva, and develops international standards in cooperation with national standard organizations of approximately 160 countries. ISO defines standards in various areas such as quality, safety, environment, and occupational health for products and services. These standards offer significant benefits such as streamlining business processes, reducing risks, increasing efficiency, and providing competitive advantages in the global market.
ISO certification officially proves that an organization operates in compliance with specific standards. Obtaining an ISO certificate instills confidence in customers and business partners and demonstrates that the quality management system is approved. Particularly in competitive markets and international trade, compliance with ISO standards enhances the reliability and prestige of a company. In short, ISO helps establish a culture of quality within organizations while also increasing global recognition.
2. Which Companies Should Obtain ISO Certification?
The ISO certificate is valuable for companies operating in a wide range of sectors, from manufacturing to services. The following situations may necessitate ISO certification:
Manufacturing and production sector: Companies aiming to standardize production quality, build trust in the supply chain, and access international markets.
Service sector: Businesses such as hotels, hospitals, software companies seeking to certify the quality of their services.
Food and agricultural enterprises: Producers who want to ensure food safety standards and build trust through ISO 22000 or ISO 9001 certification.
Information technology and finance sector: Technology firms looking to build client trust through standards such as ISO 27001 for information security or ISO 20000 for service management.
Healthcare, education, and public institutions: Organizations seeking to certify process and quality management, employee safety, and service standards.
Those participating in public tenders or aiming for export: Many public tenders and international supply contracts require an ISO certificate; hence, companies aiming to bid or export often need this certification.
Enterprises of all sizes: Small and medium-sized enterprises (SMEs) seeking to gain corporate prestige or become part of the supply chain of large corporations can increase their competitiveness by obtaining ISO certification.
3. Main ISO Standards
ISO 9001 (Quality Management System)ISO 9001 is the most widely used quality management system standard globally. This standard requires an organization to establish a customer satisfaction-oriented quality policy and continuously improve its processes. ISO 9001 operates within the framework of the Plan-Do-Check-Act (PDCA) cycle; by defining processes, measuring performance, and implementing improvement steps, the efficiency of the business increases. The ISO 9001 certificate documents that an organization's quality management practices comply with international standards and enhances its reputation.
ISO 14001 (Environmental Management System)ISO 14001 is a standard designed to help organizations control their environmental impact and improve environmental management. Elements that affect environmental performance, such as waste management, energy efficiency, and natural resource usage, are addressed under this standard. Within the scope of ISO 14001, environmental risks are identified, legal requirements are complied with, and sustainability principles are integrated into the business culture. The Environmental Management System certificate offers a significant advantage, especially for companies operating in environmentally sensitive sectors.
ISO 45001 (Occupational Health and Safety Management System)ISO 45001 is an international standard created to systematically manage occupational health and safety risks. It aims to minimize workplace accidents and occupational diseases, ensure employee safety, and establish a safety culture. The standard requires the definition of occupational health and safety policies, conducting risk analyses, planning preventive measures to eliminate hazards, and ensuring employee participation. The ISO 45001 certificate documents safe working conditions in the workplace and improves both employee motivation and corporate reputation.
Other Common ISO Standards
Organizations can apply for different ISO standards based on their industry and priorities. Some of the other prominent standards are:
ISO 22000 (Food Safety Management System): Ensures reliable food production by providing hygiene, traceability, and risk control throughout food production and processing.
ISO 27001 (Information Security Management System): Defines the necessary criteria for organizations to protect their information assets, manage security risks, and establish information security policies.
ISO 50001 (Energy Management System): Facilitates the establishment of energy management processes to increase energy efficiency, reduce energy costs, and minimize environmental footprint.
ISO 13485 (Quality Management System for Medical Devices): Sets quality and safety standards for medical device manufacturers and suppliers, aiming for patient safety and legal compliance.
ISO 10002 (Customer Satisfaction Management System): Provides guidance for increasing the effectiveness of complaint management processes and handling customer complaints quickly and satisfactorily.
ISO 22301 (Business Continuity Management System): Recommends planning ahead and developing continuity strategies to ensure uninterrupted business processes during crises and emergencies.
4. Certification Process
Preparation, application, and audit stages for ISO certification
The ISO certification process generally consists of the following key steps:
1. Preliminary Preparation: The organization determines the required standard(s) and performs a current situation analysis. During this stage, internal training is provided, and quality policies and objectives are defined. Existing documents and processes are reviewed to identify deficiencies. A roadmap is then prepared to plan the upcoming steps.
2. Application: A suitable certification body is selected, and an application is submitted. For example, during the ISO 9001 application phase, the company presents key documents such as the quality manual, process map, and quality policy, along with the organizational structure, to the certification body. The scope and costs of the audit are determined, and a contract is signed.
3. Documentation: A quality manual, procedures, instructions, and forms are prepared in accordance with the selected ISO standard. How each process and department is managed is documented. At this stage, internal audits are conducted, and management review meetings are held. Training is completed, deficiencies are identified and corrected. The system is thus made ready for implementation.
4. Audit: The certification body conducts a two-phase audit: a preliminary audit (document review) and the main audit. The preliminary audit checks whether the documents meet the standard requirements. During the main audit, auditors examine on-site processes, interview employees, and verify the existence of records. If nonconformities are found, the organization implements corrective actions, and a re-evaluation may be performed.
5. Certification: If the audit is successful, a compliance report is issued, and the certificate is granted. The ISO certificate proves full compliance with the standard. The certificate is typically valid for 3 years, during which annual surveillance audits are conducted.
6. Surveillance Audits: Annual surveillance audits are conducted throughout the certificate’s validity. During these audits, the performance of the quality management system is monitored, new objectives are set, and continuous improvement is ensured. At the end of the three-year period, a recertification audit is conducted, and the certificate is renewed.
Throughout the certification process, it is crucial that documentation is complete and that all stakeholders are involved. Coordination with the certification body helps ensure a smooth process and allows any deficiencies to be corrected before the audit.
5. Tips for a Successful Certification
A meticulous preparation process is essential for success in ISO certification. There are important points to consider at each stage; the following suggestions will help ensure the certification process runs smoothly:
Common mistakes:Lack of management support: When top management does not participate in quality and process management, it prevents the establishment of a quality culture within the organization.
Incomplete or outdated documentation: Missing or outdated procedures, instructions, and records can create problems during the audit.
Lack of employee training: Employees not being sufficiently informed about quality objectives, processes, and responsibilities is a significant deficiency.
Failure to conduct internal audits and management reviews: Not carrying out regular internal audits or holding management review meetings can result in unnoticed system errors.
Failure to follow corrective/preventive actions: Not taking necessary corrective and preventive actions for identified nonconformities can lead to recurring issues.
Oversimplifying processes: Over-simplifying business processes or not documenting them can result in failure to meet standard requirements.
Pre-audit checklist:
Are documents ready? Ensure that all procedures, the quality manual, and record forms are complete and up-to-date.
Has training and awareness been provided? Are employees adequately informed about ISO requirements, company policies, and process responsibilities? Are training records available?
Has an internal audit been conducted? Was an internal audit carried out before certification, and were nonconformities identified and corrected?
Was a management review conducted? Were quality objectives evaluated, performance indicators reviewed, and necessary improvement decisions made?
Are quality objectives and indicators defined? Have performance criteria been determined and are they being monitored?
Have corrective and preventive actions been completed? Were previously identified deficiencies corrected, and are records available?
Are business processes defined? Are the main business processes, responsible parties, and measurement points clearly identified?
Have nonconformities been resolved? Were all identified nonconformities addressed and recorded properly?
Are you informed about the certification process? Have you obtained information about the requirements and timeline of the selected certification body? Have certification costs been included in planning?
By paying attention to these suggestions, organizations can reduce the risk of unexpected issues during audits and become eligible to receive their ISO certificate more quickly.
6. Advantages Offered by Kioscert
International certification experience and customer-oriented service approach
Areas of Expertise: Kioscert offers certification services in a wide range of areas including quality management, environment, and occupational health and safety. In addition to core standards such as ISO 9001 Quality Management System, ISO 14001 Environmental Management System, and ISO 45001 Occupational Health and Safety, it also specializes in fields like ISO 22000 (Food Safety) and ISO 27001 (Information Security). With its experience in sectors such as food, healthcare, textiles, and technology, it provides tailored solutions to meet the needs of every organization.
Fast Process Management: Kioscert conducts the ISO certification process through effective project management. Its expert team plans according to the process timeline and completes steps promptly. All stages, from determining certification requirements to scheduling the audit, are meticulously organized. As a result, the certification process is accelerated, and organizations receive their ISO certificates more quickly.
Thanks to these advantages, certification projects with Kioscert are completed more systematically and on time, allowing businesses to confidently fulfill all requirements of the ISO certification process.